Expert Techniques for Achieving Ultra-Smooth Finishes in Metal CNC Turning
- Pailin Laser Metal Team
- Apr 30
- 3 min read
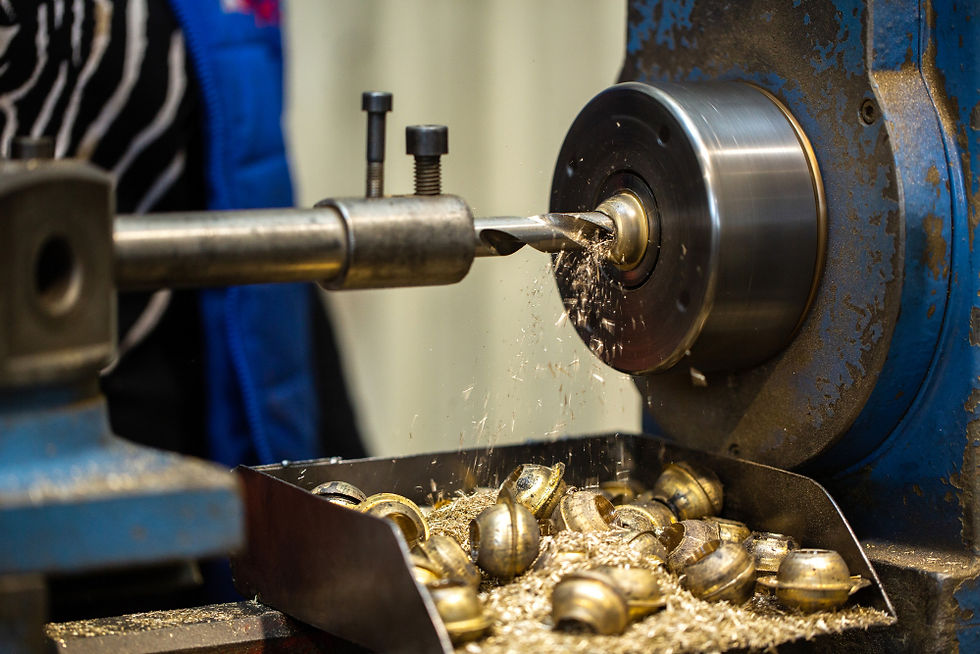
Ever wondered why some machined parts have glass-like finishes while others show scratches or uneven textures? The difference lies not just in the machine itself, but in the metal CNC turning techniques used by the operator. In today’s increasingly competitive manufacturing landscape, surface finish isn’t just a nice-to-have—it’s a necessity.
This article reveals the expert tips and techniques used in CNC turning to produce flawless surface finishes, reduce defects, and boost production efficiency. From understanding key influencing factors to applying advanced strategies, you’ll gain the knowledge needed to take your metal CNC work to the next level.
Choosing the Right Cutting Tool
The foundation of a smooth finish in metal CNC turning starts with selecting the right cutting tool. First, the tool material must match the workpiece. For hard materials like steel, carbide or CBN (Cubic Boron Nitride) tools are ideal for their wear resistance. For softer metals like aluminum, HSS (High-Speed Steel) tools are often sufficient.
Tool geometry also plays a critical role. A smaller nose radius, for example, results in finer finishes but requires lower feed rates. Rake angles and clearance angles help improve chip flow, reduce heat buildup, and prevent scratches. Additionally, coated tools (e.g., TiN, TiCN, TiAlN) offer increased hardness and lower friction, extending tool life and enhancing finish quality.
Optimizing Cutting Conditions
Beyond tool selection, cutting parameters must be finely tuned. Higher cutting speeds generally yield better finishes, but excessive speed can overheat the tool and degrade surface quality. Feed rate also matters—slower feeds produce smoother surfaces but may slow down production. Balance is key.
Depth of cut is another factor: while rough turning uses deeper cuts for efficiency, finishing should use shallow passes to minimize vibration and achieve smoother surfaces.
Using Coolant Effectively
Coolant does more than regulate temperature in metal CNC operations—it also helps achieve better surface finishes. Choosing the right coolant type for both the material and tool is crucial. Proper lubrication reduces friction and heat, which protects the tool and the workpiece.
Coolant also washes away metal chips that could otherwise scratch the surface. For best results, ensure adequate flow and pressure so the coolant fully covers the cutting zone, enhancing both cooling and lubrication.
The Importance of Finishing Passes
To achieve a superior surface finish, a dedicated finishing pass is essential. After rough turning removes most of the material, finishing involves ultra-sharp tools with geometries optimized for fine work—such as tools with smaller nose radii or Wiper Inserts designed to smooth out surfaces.
In finishing, parameters change drastically: minimal depth of cut, low feed rates, and appropriate cutting speeds reduce cutting forces and vibrations. The result is a smooth, shiny, and dimensionally precise surface.
Minimizing Vibration
Vibration is the enemy of a smooth CNC-turned finish. It can cause ripples, chatter marks, or inconsistent textures. Begin by ensuring solid machine setup—both tool and workpiece must be clamped tightly with no play.
Use tools designed to minimize vibration, such as those with optimized rake and relief angles or internal damping systems. Avoid cutting parameters that trigger chatter; sometimes, reducing depth of cut or using multiple light passes can help.
Writing the Right G-Code
Even with perfect tools and setup, improper G-code can ruin a finish. Smooth toolpaths are essential—abrupt speed or direction changes cause visible marks.
Use G02/G03 for curved movements instead of stitching together multiple G01 (linear) commands. Many modern CNC controllers support Look-Ahead or Smoothing functions, allowing machines to anticipate and smooth transitions, which significantly improves surface quality.
Final Thoughts: Mastering the Art of Metal CNC Finishing
Achieving an ultra-smooth surface in metal CNC turning is a fusion of science and art—combining material knowledge, tool selection, precise parameter tuning, and environmental control.
If you're seeking a partner to help elevate the finish quality of your machined parts, Pailin Laser Metal (PLM) is ready to deliver. With extensive experience and a passion for high-performance metalwork, we bring your vision to life with premium-quality results.
Let PLM be the finishing touch your CNC projects deserve.
Comments