7 Key Reasons Why Laser Cutting Has Become the Heart of Automotive Manufacturing
- Pailin Laser Metal Team
- Jun 4
- 4 min read
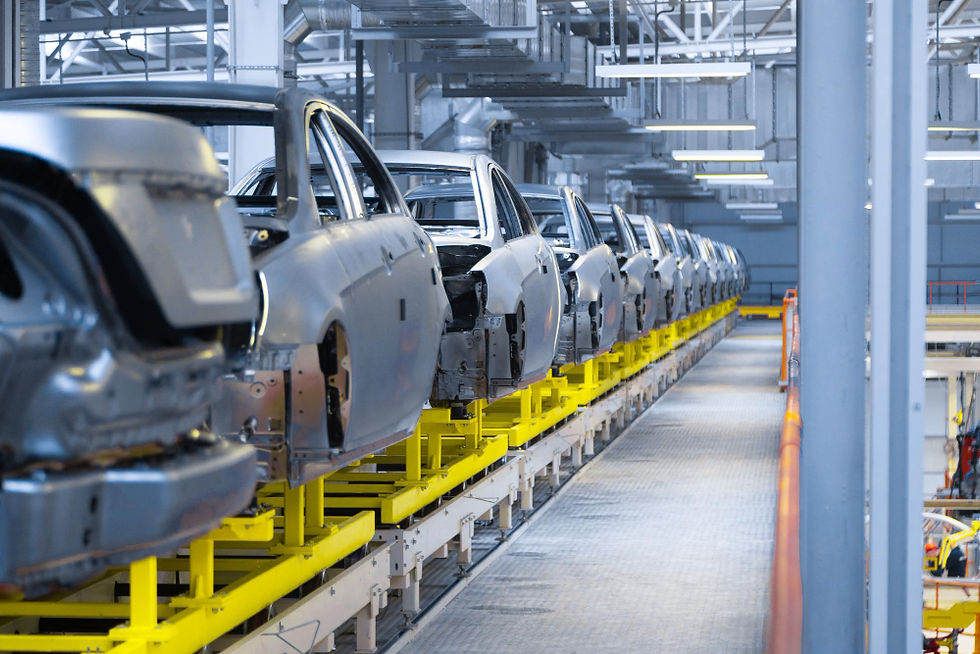
In the fiercely competitive automotive industry—where innovation, speed, and precision are the keys to success—manufacturing technology determines who leads the pack. Laser cutting has emerged as a transformative tool, not just an option but a core technology driving the creation of modern vehicles. Here are 7 crucial reasons why laser cutting is so influential—and why it has become indispensable to automotive manufacturing today.
1. Unmatched Precision and Accuracy
Laser cutting delivers micrometer-level precision:
Perfect Fit for Components:Automotive parts—body panels, structural frames, or interior components—must fit together seamlessly. High-precision cutting minimizes gaps, making assembly easier, faster, and consistently high quality, with fewer reworks.
Enhanced Safety and Performance:Even the slightest deviation in critical parts like chassis frames or mounting points can affect vehicle safety and performance. Laser cutting ensures parts are made exactly to design specifications.
Complex Designs Supported:Modern car designs often involve intricate shapes and fine details. Laser cutting handles these with pinpoint accuracy, like cutting puzzle pieces that fit perfectly—essential for smooth assembly and top-notch safety.
2. Superior Production Speed and Efficiency
Laser cutting stands out for its speed and efficiency:
Faster Cutting:Especially with thin to medium-thickness metals, lasers move and cut faster than most mechanical methods, significantly reducing production time per part.
Shorter Lead Times:Faster cuts mean more components or vehicles produced in the same time frame.
Higher Output:Manufacturers can meet high, fluctuating market demand with greater flexibility.
Reduced Waiting Times:Faster production means quicker delivery of vehicles to customers or parts to the next assembly stage.
3. Exceptional Design and Production Flexibility
Laser cutting offers unrivaled flexibility:
No Need for Dies:Design changes are easy—just update the CAD file, with no need to invest in costly metal-stamping dies.
Ideal for Prototypes:Quickly produce test parts or prototype vehicles, accelerating R&D and speeding time-to-market for innovations.
Adaptable for Various Production Volumes:Whether producing a few parts for a special edition or large-scale mass production, the same laser equipment can handle it—streamlining production planning.
Custom Creations:Manufacturers can easily produce complex designs or customer-specific parts, enhancing product differentiation.
In essence, laser cutting acts like a “metal 3D printer,” enabling quick adjustments and production runs from one prototype to full-scale production—all without the hassle of physical dies.
4. Superior Cut Quality Reduces Post-Processing
Laser cutting provides top-notch quality and minimizes extra steps:
Clean, Precise Cuts:Smooth edges with minimal burrs or dross result in high-quality finishes.
Narrow Heat-Affected Zone:Heat from cutting impacts only a small area, preserving material properties like strength—critical for safety.
Minimal Finishing Work:Because of the quality cuts, there’s little need for additional grinding or deburring, speeding up production.
Ready for the Next Step:Laser-cut parts are often ready for welding, assembly, or painting immediately, reducing production bottlenecks.
It’s like having the sharpest, most precise knife—cutting with accuracy and efficiency that preserves the integrity of every part.
5. Ability to Cut a Wide Range of Materials
Laser cutting excels in versatility:
Cuts Both Metals and Non-Metals:From various steels (including high-strength AHSS popular for weight reduction) and stainless steel to aluminum, plastics, composites (e.g., carbon fiber), upholstery fabrics, leather, and even rubber—lasers can handle it all (with the right laser type or settings).
Supports Automotive Trends:Modern cars use mixed materials for lightweighting, strength, and aesthetics. Lasers meet this demand head-on.
Simplifies Production:Instead of using multiple specialized machines for each material, one laser can handle nearly everything—streamlining the production line.
In short, lasers are like a “universal cutting tool” for car manufacturing, capable of processing nearly every material that makes up a modern vehicle.
6. Reduces Costs Across the Board
Laser cutting significantly lowers manufacturing costs:
Saves Material:High precision and efficient nesting mean minimal waste and optimal material use, cutting down on scrap compared to other methods.
No Die Costs:Eliminates the need to build, store, and maintain expensive metal-stamping dies—especially helpful for low-volume production, prototypes, or frequent design changes.
Reduced Labor Costs:High-quality cuts require less post-cutting finishing like deburring or grinding—tasks that often need manual labor. Easier integration with robotics also reduces reliance on manual processes.
Time Savings (Time is Money):Faster cuts and no die changes mean quicker production, slashing overall operating costs.
Fewer Errors:High precision means fewer rejected parts or reworks.
Laser cutting delivers savings at every stage—from materials and die costs to labor, time, and quality—boosting overall competitiveness.
7. Fosters Innovation and Complex Designs
Laser cutting opens the door to cutting-edge innovation:
No Die Constraints:Designers aren’t limited by complex die requirements or high die costs—lasers cut directly from digital files.
Freedom of Shape:Easily cuts highly curved lines, intricate patterns, and complex geometric shapes—allowing for eye-catching automotive designs.
Accelerates Prototyping:Quickly create prototype parts from digital designs, letting designers test, refine, and validate concepts faster—speeding the innovation cycle.
Handles Advanced Materials:Cuts composite materials, special alloys, and other advanced materials—enabling lightweight, strong structures and unique designs.
Laser cutting is like a “digital pen” empowering designers to bring bold ideas to life without production limitations—enabling next-generation cars filled with creativity and innovation.
Conclusion
These 7 reasons clearly show why laser cutting isn’t just an add-on but a core technology driving today’s automotive industry. From producing the most precise parts and dramatically improving production efficiency to unlocking design freedom and reducing costs, laser cutting is the answer to today’s—and tomorrow’s—manufacturing challenges.
If you’re looking to bring the limitless potential of laser cutting to your automotive business, Pailin Laser Metal Co., Ltd. is your answer. With expertise and experience, we “cut every obstacle and create every possibility,” ensuring your parts meet the highest standards of precision, quality, and speed. Let Pailin Laser Metal drive your success toward excellence in the automotive industry.
Commenti