เทคนิคการกลึง CNC ให้ได้ผิวงานที่เรียบเนียน
- Pailin Laser Metal Team
- 13 เม.ย.
- ยาว 1 นาที
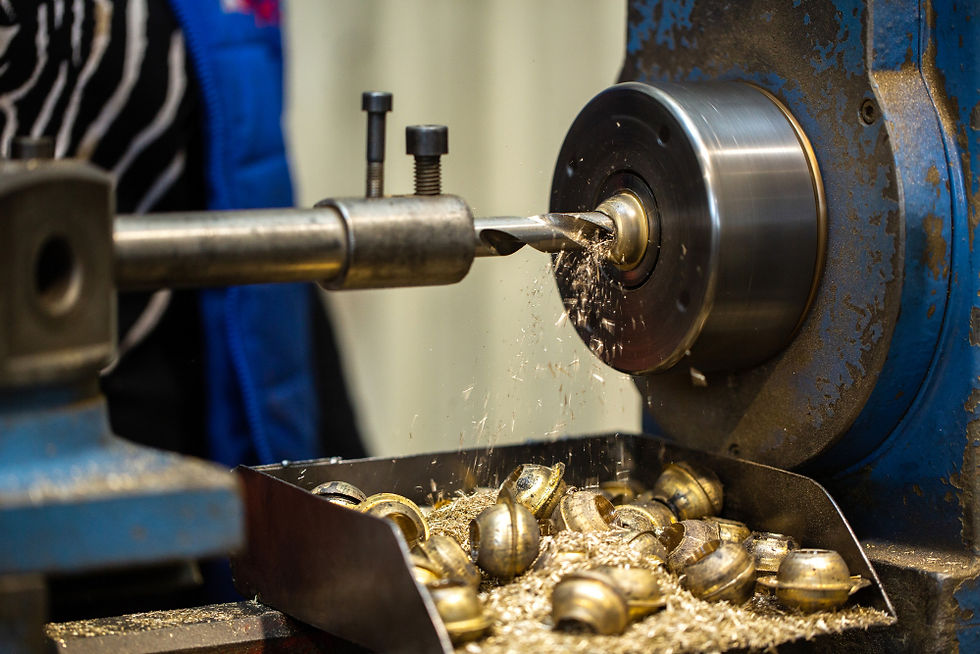
คุณเคยสงสัยไหมว่า ทำไมชิ้นส่วนบางชิ้นถึงมีผิวที่เรียบเนียนราวกับกระจก ในขณะที่บางชิ้นกลับมีรอยขีดข่วนหรือผิวที่ไม่สม่ำเสมอ คำตอบไม่ได้อยู่ที่เครื่องจักรเพียงอย่างเดียว แต่อยู่ที่ "เทคนิค" การกลึง CNC ที่ผู้ปฏิบัติงานเลือกใช้ ในอุตสาหกรรมการผลิตที่การแข่งขันสูงขึ้นเรื่อย ๆ การมีผิวสำเร็จที่เหนือกว่าไม่ได้เป็นเพียงข้อได้เปรียบ แต่เป็นสิ่งจำเป็น
บทความนี้จะเปิดเผยเคล็ดลับและเทคนิคที่ผู้เชี่ยวชาญใช้ในการกลึง CNC เพื่อให้ได้ผิวงานที่เรียบเนียน ลดข้อบกพร่อง และเพิ่มประสิทธิภาพในการผลิต ตั้งแต่การทำความเข้าใจปัจจัยที่มีผลต่อผิวสำเร็จ ไปจนถึงการประยุกต์ใช้เทคนิคขั้นสูง คุณจะได้เรียนรู้ทุกสิ่งที่คุณจำเป็นต้องรู้เพื่อก้าวไปสู่ความเป็นเลิศในการกลึง CNC
เทคนิคการกลึง CNC ให้ได้ผิวงานเรียบเนียน
ผิวสำเร็จที่เรียบเนียนในการกลึง CNC ไม่ได้เกิดขึ้นเอง แต่เป็นผลลัพธ์ของการผสมผสานเทคนิคที่ถูกต้อง ตั้งแต่การเลือกเครื่องมือ วัสดุ ไปจนถึงการตั้งค่าพารามิเตอร์ บทความนี้จะเปิดเผยเคล็ดลับสำคัญสู่ผิวงาน CNC ที่ไร้ที่ติ
การเลือกใช้เครื่องมือตัดที่เหมาะสม
การเลือกใช้เครื่องมือตัดที่เหมาะสมถือเป็นหัวใจสำคัญของการกลึง CNC ให้ได้ผิวงานที่เรียบเนียนอย่างแท้จริง ประการแรก วัสดุของเครื่องมือตัดต้องสอดคล้องกับวัสดุชิ้นงาน หากกลึงวัสดุแข็ง เช่น เหล็กกล้า ควรเลือกใช้เครื่องมือตัดจำพวกคาร์ไบด์ (Carbide) หรือ CBN (Cubic Boron Nitride) ซึ่งมีความแข็งสูง ทนต่อการสึกหรอได้ดี ในทางกลับกัน หากกลึงวัสดุอ่อน เช่น อะลูมิเนียม อาจเลือกใช้เครื่องมือตัด HSS (High-Speed Steel) ได้
ประการต่อมา รูปทรงของเครื่องมือตัดมีบทบาทสำคัญ โดยเฉพาะ "รัศมีปลายมีด" (Nose Radius) ที่มีขนาดเล็กจะช่วยลดแรงตัดและสร้างผิวสำเร็จที่ละเอียดกว่า แต่ต้องแลกมาด้วยอัตราป้อนที่ต่ำลง นอกจากนี้ มุมคาย และมุมหลบ ที่เหมาะสมจะช่วยให้การคายเศษเป็นไปอย่างราบรื่น ลดการสะสมความร้อน และลดโอกาสที่เศษจะไปขูดขีดผิวชิ้นงาน สุดท้าย การเคลือบผิวเครื่องมือตัดด้วยวัสดุพิเศษ เช่น TiN, TiCN, หรือ TiAlN สามารถเพิ่มความแข็ง ลดแรงเสียดทาน และยืดอายุการใช้งานของเครื่องมือตัด ซึ่งส่งผลโดยตรงต่อคุณภาพผิวสำเร็จที่ได้
อ่านเพื่อมเติมเกี่ยวกับ เครื่องกลึง CNC
การตั้งค่าเงื่อนไขการตัดที่เหมาะสม
นอกเหนือจากการเลือกเครื่องมือตัดแล้ว การตั้งค่าเงื่อนไขการตัด (Cutting Conditions) ที่เหมาะสมก็มีความสำคัญอย่างยิ่งต่อการได้มาซึ่งผิวสำเร็จที่เรียบเนียนในการกลึง CNC เริ่มต้นด้วย "ความเร็วตัด" ที่สูงขึ้นโดยทั่วไปจะช่วยให้ผิวงานละเอียดขึ้น แต่ต้องระวังไม่ให้สูงเกินไปจนเครื่องมือตัดสึกหรอเร็ว หรือเกิดความร้อนสะสมมากเกินไป ซึ่งจะส่งผลเสียต่อผิวสำเร็จและอายุการใช้งานของเครื่องมือ
ต่อมาคืออัตราป้อนหรือความเร็วที่เครื่องมือตัดเคลื่อนที่ไปตามผิวชิ้นงาน ก็มีผลอย่างมากเช่นกัน อัตราป้อนที่ต่ำจะให้ผิวสำเร็จที่ละเอียดกว่า แต่ก็ต้องแลกมาด้วยเวลาในการผลิตที่นานขึ้น การหาจุดสมดุลระหว่างความเร็วตัดและอัตราป้อนจึงเป็นสิ่งสำคัญ
สุดท้ายคือระยะกินลึก (Depth of Cut) ในการกลึงหยาบ ควรใช้ระยะกินลึกที่มากพอสมควรเพื่อประสิทธิภาพในการผลิต แต่สำหรับการกลึงละเอียด ควรลดระยะกินลึกลงให้เหลือน้อยที่สุด เพื่อลดแรงตัดและแรงสั่นสะเทือน ซึ่งจะช่วยให้ได้ผิวสำเร็จที่เรียบเนียนสูงสุด
การใช้น้ำหล่อเย็นอย่างถูกต้อง
น้ำหล่อเย็น ไม่ได้มีไว้เพียงแค่ลดอุณหภูมิในการกลึง CNC เท่านั้น แต่ยังมีบทบาทสำคัญในการช่วยให้ได้ผิวสำเร็จที่เรียบเนียนอีกด้วย การเลือกใช้น้ำหล่อเย็นที่เหมาะสมกับวัสดุชิ้นงานและประเภทของเครื่องมือตัดเป็นสิ่งแรกที่ต้องพิจารณา น้ำหล่อเย็นจะทำหน้าที่หล่อลื่น ลดแรงเสียดทานระหว่างเครื่องมือตัดและชิ้นงาน ซึ่งช่วยลดการเกิดความร้อนสะสมและการสึกหรอของเครื่องมือตัด
นอกจากนี้ น้ำหล่อเย็นยังช่วยชะล้างเศษโลหะที่เกิดจากการตัดเฉือนออกจากบริเวณที่ทำการตัด ป้องกันไม่ให้เศษเหล่านี้ไปขูดขีดผิวงานจนเกิดเป็นรอยหรือตำหนิ การปรับปริมาณและแรงดันของน้ำหล่อเย็นให้เหมาะสมก็สำคัญเช่นกัน ควรให้น้ำหล่อเย็นไหลผ่านบริเวณที่ทำการตัดอย่างทั่วถึงและสม่ำเสมอ เพื่อให้มั่นใจว่าทั้งเครื่องมือตัดและชิ้นงานได้รับการหล่อเย็นและหล่อลื่นอย่างเต็มที่
การกลึงละเอียด
เพื่อให้ได้ผิวสำเร็จขั้นสุดท้ายที่เรียบเนียนระดับสูงสุดในการกลึง CNC เทคนิค "การกลึงละเอียด" (Finishing) เป็นขั้นตอนที่ขาดไม่ได้ หลังจากผ่านกระบวนการกลึงหยาบ (Roughing) เพื่อขจัดเนื้อวัสดุส่วนใหญ่ออกไปแล้ว การกลึงละเอียดจะใช้เครื่องมือตัดที่มีความคมสูง และมีรูปทรงที่ออกแบบมาเพื่องานละเอียดโดยเฉพาะ เช่น มีดกลึงที่มีรัศมีปลายมีดเล็ก หรือ Wiper Inserts ที่มีขอบตัดพิเศษช่วยปรับผิวให้เรียบ
เงื่อนไขการตัดในการกลึงละเอียดจะแตกต่างจากการกลึงหยาบอย่างชัดเจน โดยจะใช้ระยะกินลึกที่น้อยมาก (ตื้นมากๆ) อัตราป้อนต่ำ และความเร็วตัดที่เหมาะสมกับวัสดุชิ้นงานและเครื่องมือตัด การตั้งค่าเหล่านี้จะช่วยลดแรงตัด ลดการสั่นสะเทือน และป้องกันการเกิดรอยบนผิวชิ้นงาน ผลลัพธ์ที่ได้คือผิวสำเร็จที่มีความเรียบเนียน เงางาม และมีความแม่นยำตามแบบที่ต้องการ
การหลีกเลี่ยงการสั่นสะท้าน
การสั่นสะท้าน เป็นศัตรูตัวฉกาจของผิวสำเร็จที่เรียบเนียนในการกลึง CNC เพราะการสั่นสะท้านจะทำให้เกิดรอยคลื่นบนผิวชิ้นงาน การควบคุมและหลีกเลี่ยงการสั่นสะท้านจึงมีความสำคัญอย่างยิ่ง เริ่มต้นจากการตรวจสอบความมั่นคงแข็งแรงของเครื่องจักรและระบบจับยึด ทั้งชิ้นงานและเครื่องมือตัดต้องถูกจับยึดอย่างแน่นหนา ไม่มีการโยกคลอน
การเลือกใช้เครื่องมือตัดที่มีคุณภาพและมีการออกแบบเพื่อลดการสั่นสะเทือน เช่น เครื่องมือตัดที่มีมุมคายและมุมหลบที่เหมาะสม หรือมีระบบ Dampening ในตัว ก็สามารถช่วยลดปัญหาได้ นอกจากนี้ การปรับตั้งค่าพารามิเตอร์การตัดอย่างเหมาะสม โดยเฉพาะอย่างยิ่งการหลีกเลี่ยงความเร็วตัดและอัตราป้อนที่ก่อให้เกิดการสั่นสะเทือน ก็เป็นสิ่งจำเป็น หากจำเป็น อาจต้องลดระยะกินลึก หรือใช้เทคนิคการกลึงแบบหลายรอบ (Multiple Passes) เพื่อลดภาระการตัดและลดโอกาสที่จะเกิดการสั่นสะท้าน
การใช้ G-Code ที่เหมาะสม
แม้จะมีเครื่องมือและการตั้งค่าที่ยอดเยี่ยมเพียงใด หาก G-code ที่ใช้ควบคุมเครื่องกลึง CNC ไม่เหมาะสม ก็ยากที่จะได้ผิวงานที่เรียบเนียน G-code ที่ดีควรมีการเคลื่อนที่ของเครื่องมือตัดที่ราบรื่นและต่อเนื่อง หลีกเลี่ยงการเปลี่ยนแปลงทิศทางหรือความเร็วอย่างกะทันหัน ซึ่งอาจทำให้เกิดรอยต่อหรือรอยสะดุดบนผิวชิ้นงาน
การใช้คำสั่ง G02/G03 (Circular Interpolation) สำหรับการเคลื่อนที่เป็นเส้นโค้ง แทนการใช้ G01 (Linear Interpolation) หลาย ๆ คำสั่ง จะช่วยให้การเคลื่อนที่นุ่มนวลขึ้น นอกจากนี้ การใช้ฟังก์ชัน Look-Ahead หรือ Smoothing ที่มีในคอนโทรลเลอร์ CNC รุ่นใหม่ ๆ จะช่วยให้เครื่องจักรมองล่วงหน้า และปรับการเคลื่อนที่ให้เหมาะสม ลดโอกาสที่จะเกิดการกระตุกหรือหยุดชะงักระหว่างการตัดเฉือน ซึ่งจะส่งผลโดยตรงต่อคุณภาพผิวสำเร็จที่ได้
การกลึง CNC ให้ได้ผิวงานที่เรียบเนียน คือการผสานรวมทั้งศาสตร์และศิลป์ ตั้งแต่ความเข้าใจในวัสดุศาสตร์ การเลือกใช้เครื่องมือที่เหมาะสม การตั้งค่าพารามิเตอร์อย่างแม่นยำ ไปจนถึงการควบคุมปัจจัยแวดล้อมต่าง ๆ หากคุณกำลังมองหาผู้เชี่ยวชาญที่จะช่วยยกระดับคุณภาพผิวสำเร็จของชิ้นงานของคุณ ให้ ไพลิน เลเซอร์ เมทเทิล PLM เป็นคำตอบ ด้วยประสบการณ์และความมุ่งมั่นในการสร้างสรรค์งานโลหะระดับพรีเมียม เราพร้อมที่จะ "เจียระไน" ทุกความต้องการของคุณให้เป็นจริง
ความคิดเห็น